About the Program
The objective of this Process Safety Engineering course is to provide the candidates the Detail knowledge and skills in Process Safety Engineering discipline to facilitate faster learning curves while on the job.
The course is designed to accelerate the participant’s process safety learning curve. Serious process safety incidents occur somewhere in the industry nearly every week, and few if any are new; essentially the same ways of going wrong are found repeatedly, in different operating contexts. One of the main objectives of this Course is to develop knowledge of the more common ways of going wrong, and one of the ways of doing that is the discussion of major incidents, including some of those that have affected our regulatory environment. With this course graduate should be able to see their facilities and projects with a new perspective, a new sense of not only how things work, but also of how things fail. They will also have an appreciation of the reasons for some of our process safety practices and regulations, which will contribute to the more consistent and better-reasoned application of them.
Learning objective
- Describe the overall production chain and explain the main techniques and equipment used in the Oil & Gas facilities,
- Detail process safety elements and purpose,
- Describe process safety management roles and responsibilities,
- Contribute to process hazard analysis studies, events analysis, and investigative reporting and monitoring,
- Develop leadership techniques to enhance the safety culture in the organization.
- Thinking in terms of Inherently Safer Design
- Most common process hazard analysis methods and where they are used
- Layers of Protection concept – what the different layers are and how they are applied
Program Highlights
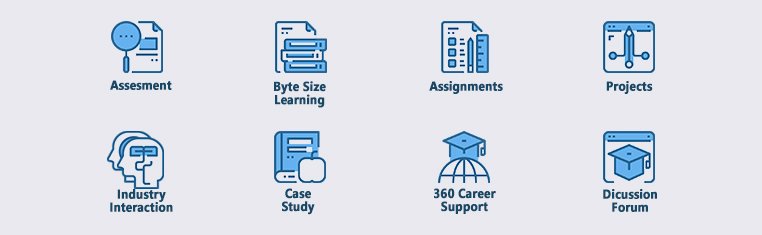
About The Course
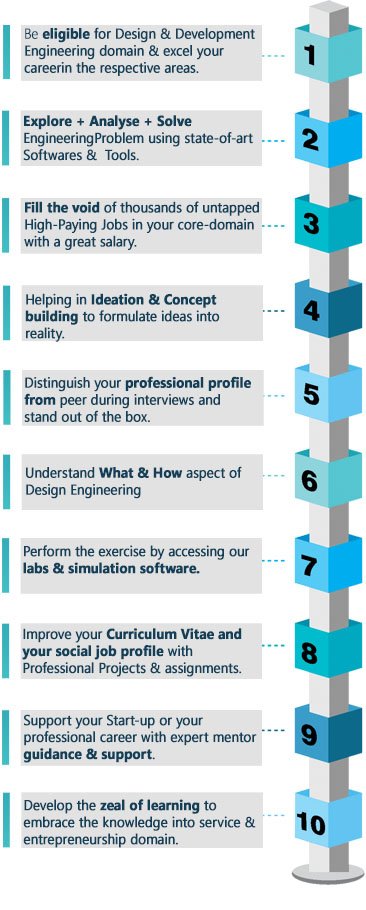
Course Modules
- OIL & GAS FIELD PROCESSING
- Fundamentals of reservoir engineering, drilling, completion and well servicing.
- Fundamentals of thermodynamics applied to effluent processing.
- Crude oil treatment.
- Production water treatment and injection.
- Gas processing and conditioning.
- Overview of static equipment- Piping, valves, thermal and storage equipment.
- Overview of rotating equipment- Pumps, compressors and gas turbines
- SAFETY ENGINEERING:-Advanced Techniques
- Inherently safer plant design
- Consequence analysis methodology
- Quantitative Risk Assessment (QRA)
- Safety Instrumented Systems (SIS)
- Design of fire and gas detection systems
- Active and passive fire protection
- Human factors and human errors
- Safety engineering mini-project for a specific surface production facility
- Hazard identification: HAZID/HAZOP
- Major hazard assessment
- Consequence analysis
- Plant layout
- QRA
- Safety Instrumented Systems (SIS)
- Fire protection and emergency response
- INTRODUCTION TO PROCESS SAFETY MANAGEMENT:-
- Concept of process safety
- Historical approach
- Process safety roles and responsibilities
- Safe design principles
- Introduction to inherently safer design
- Concept of loss of containment
- Fundamentals of flammability and fluid behavior
- Major accident hazards
- Introduction to bowtie diagram representation
- PROCESS SAFETY REGULATIONS
- Identification and compliance with legislation and industry standards
- Best practices standards: OSHA, CCPS
- Relationship with other benchmarking standards: offshore safety case regulation, SEVESO III
- PROCESS SAFETY CULTURE
- Safety leadership and commitment
- Safety culture
- Workforce involvement
- Stakeholder’s identification and communication
- PROCESS HAZARD ANALYSIS
- Process safety information: products, technology, equipment and human intervention
- Hazards related to typical Oil & Gas process
- Methodology for carrying out a HAZID
- HAZID application
- Introduction to HAZOP methodology
- Node identification
- Guidewords
- HAZOP register matrix
- Group management
- Introduction to What-if methodology
- HAZOP exercise
- Introduction to Failure Mode and Equipment Analysis (FMEA study)
- Introduction to fault tree analysis
- Plant layout
- OPERATING PROCEDURES
- Definition of operating phase steps and limits
- Process monitoring
- Process control system elements
- Safe isolation of equipment
- Pre-startup safety review
- Operational readiness
- Case study: Buncefield
- SAFETY ENGINEERING:-Fundamentals Of Safety Engineering
- Aims of safety engineering
- Safety engineering throughout the life of a project and during operations
- Safe design principles
- Risk assessment
- Probabilistic and deterministic methods
- Concept of loss of containment
- Fundamentals of flammability
- Scenario definition
- Concept of barriers
- PRELIMINARY HAZARD ANALYSIS – HAZID
- Objectives of preliminary hazard identification during conceptual/feasibility studies
- Hazards related to typical Oil & Gas process
- Methodology for carrying out a HAZID
- HAZID application
- HAZARD & OPERABILITY – HAZOP
- Introduction to HAZOP methodology
- Node identification
- Guidewords
- HAZOP register matrix
- HAZOP exercise
- MAJOR HAZARD ASSESSMENT
- Major Accident Hazard (MAH) scenarios
- Scenario representation. Bowtie diagrams
- Risk reduction process
-
- Risk matrices and ALARP principle
- Safety-critical measures/elements
- Major accident hazards analysis
- Tools Fault Tree Analysis (FTA) and Event Tree Analysis (ETA).
- ADVANCED TECHNIQUES
- Inherently safer plant design
- Consequence analysis methodology
- Quantitative Risk Assessment (QRA)
- Safety Instrumented Systems (SIS)
- Design of fire and gas detection systems
- Active and passive fire protection
- Human factors and human errors
- Safety engineering mini-project for a specific surface production facility
- Hazard identification: HAZID/HAZOP
- Major hazard assessment
- Consequence analysis
- Plant layout
- QRA
- Safety Instrumented Systems (SIS)
- Design of fire and gas detection systems
- Active and passive fire protection
- Human factors and human errors
- HSE IN SURFACE PRODUCTION OPERATIONS:-Operations & Hse
- Hazards and risks incurred
- Consequences
- Risk management means: equipment, organizational and human aspects
- MAIN HAZARDS OF HYDROCARBON PROCESSING
- Flammability: flame ignition and propagation principles
- Types of combustibles, oxidizers and most common ignition sources in process facilities
- Toxicity: exposure limits
- Specific hazards associated to H2S
- Use of Safety Data Sheet (SDS)
- Fluid behavior and related hazards: vessel pressure, consequences of temperature variation (thermal expansion, vaporization, vacuum, water hammer)
- Fundamentals of pressure relief equipment: pressure relief valves, rupture disks, vacuum protection, flame arrestors.
- RISK ASSESSMENT TOOLS – JOB SAFETY ANALYSIS
- Fundamentals of risk assessment process
- Job Safety Analysis (JSA) procedure and steps
- RISK IN NORMAL PROCESS OPERATIONS
- Risks associated with static equipment
- Risks associated with rotating machinery
- Risks associated with the use of utilities: inert gases, liquid water, steam, air, diesel, fuel gas
- SAFE ISOLATION OF PLANT & EQUIPMENT
- Management of isolations
- Steps of process isolations
- Valve types and issues
- Mechanical isolation methods
- Strategies for selection
- Pros and cons
- Electrical lock-out
- Degassing-inerting: steam, nitrogen, water, vacuum, work permits
- Risks associated to operations of depressurization and drainage toward: flare, slops, tanks, oily water
- Start-up: checks, accessibility and cleanliness, line up, desecration, seal tests, oil in.
- Personal Protective Equipment (PPE)
- HSE IN MAINTENANCE & CONSTRUCTION WORKS – PERMIT TO WORK SYSTEM
- Permit To Work (PTW) system
- Objectives
- Roles and responsibilities
- Process
- Risks associated to construction and maintenance works
- Lifting and rigging operations
- Access and working in confined space
- Ventilation and atmosphere analysis: oxygen content explosively, toxicity
- Works at height: ladders, scaffolding, mobile elevated working platforms
- Safe use of tools
- Radioactive sources
- ORGANIZATIONAL FRAMEWORK – HUMAN FACTORS
- Introduction to HSE management system
- Simultaneous Operations (SIMOPS) management
- Management of change
- Downgraded situations
- Learning from incidents and accidents: near misses, reporting and cause tree analysis
- Human factors in risk management, safe and unsafe habits, motivation, exemplarity, difficulties in improving safety results.
- ENVIRONMENTAL MANAGEMENT IN FIELD OPERATIONS
- Main concepts
- Tools to manage sustainability
- Potential environmental impacts in field operations
- Sustainability reporting
Course Certificates
SmartBrains is associated with The National Skill Development Corporation (NSDC) as the Training and Certification partner for various job oriented training programs across various sectors including Oil & Gas, Power, Renewable Energy, Hydrocarbon, IT & ITs, Electronics, Telecom, Agriculture, Life science etc. offering assessment based Training & certifications for a gamut of job profile.
Who should join?
- Working professionals in Domains: Site Engineering, .Construction & Commissioning operation & .Maintenance, Technicians in Process Engineering Field.
- Students (Chemical Engineering, Diploma in Chemical .Engineering) who want to develop their career in Design Engineering.
For Corporate queries
A-25, Sector-59, Noida (UP),India
Pin Code-201301
Connect with Program Advisor
training@smartbrains.com
+91 9891108002
www.smartbrains.com
Nodal Centers
Noida, Dehradun
Guwahati, Pune
Course Features
- Lecture 0
- Quiz 0
- Duration 6 Months
- Skill level All levels
- Language English
- Students 0
- Assessments Yes